Air Cleaning Blowers™ (ACBs) redefine air purification by eliminating the need for pressurized air during operation. Unlike Compressed-Air-Using “Self-Cleaning” Filter Systems (SCFs), which depend on a continuous supply of compressed air, ACBs operate independently and efficiently, simplifying air filtration.
Maintenance Made Simple
- ACBs offer a distinct advantage in ease of maintenance. While SCFs collect and require regular disposal of filtered debris, ACBs bypass this entirely by not accumulating debris in the first place. This unique design reduces downtime and eliminates waste management hassles.
Cost Efficiency
- ACBs deliver significant cost savings over SCFs. Their streamlined design and compact size translate to lower upfront purchase costs and simpler installation requirements. ACBs typically require minimal space and ductwork, further reducing setup expenses compared to SCFs.
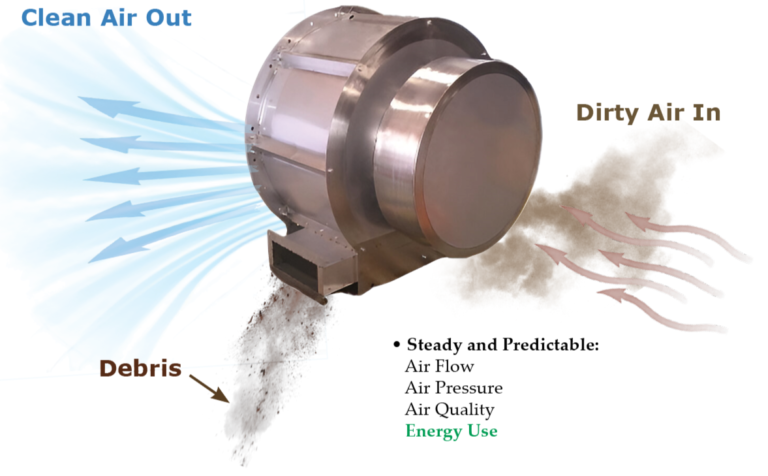
Why Choose ACBs?
Eliminate Filter Replacement Costs
- SCFs eventually need filter replacements due to clogging, leading to ongoing costs for purchasing, installing, and disposing of filter media. In contrast, ACBs—designed without filter elements—completely eliminate these recurring expenses.
Preserve Air Balance
- ACBs return separated particles back to their source, maintaining the original air and dust levels without altering the environment. While SCFs may slightly reduce dust in their immediate vicinity, their overall environmental impact is often limited to the specific application.
Energy Efficiency
ACBs excel in energy efficiency, consuming less electricity per CFM (cubic feet per minute) of airflow than SCFs. With ongoing advancements, their energy requirements continue to decrease.
- Compressed-air-based filters often operate with high pressure losses, increasing energy consumption.
- To avoid constant compressed air usage and potential filter damage, SCFs allow debris to accumulate until a pressure threshold is reached (e.g., 4″ w.g. or ~1250 Pa), triggering cleaning cycles.
- Even after cleaning, SCFs never regain their original efficiency, operating at suboptimal levels until filters are replaced.
Air Flow Performance
To provide context on pressure losses:
SCFs face compounding energy challenges as debris accumulates:
- New fan and filter elements start with low-pressure losses (~0.5″ w.g.). However, clogging can double this backpressure, increasing electrical consumption by up to 50%.
- Once SCFs reach their lower cleaning threshold (~2″ w.g.), they operate at reduced efficiency, driving up energy costs until filters are replaced.
In contrast, ACBs avoid this efficiency decline by operating without filter elements, ensuring consistent performance over time.

Waste Management Simplified
- SCFs require dust collection bins that expose workers to potential hazards during emptying and disposal. Additionally, regulations may classify collected debris as hazardous waste, incurring special disposal costs.
- ACBs sidestep these issues entirely. By not collecting or concentrating debris, they eliminate the need for handling and waste disposal, improving both safety and cost-effectiveness.
The Cost Advantage
Lower Initial and Maintenance Costs
- ACBs typically have lower upfront and installation costs compared to SCFs. They also avoid the need for complex control systems like Variable Frequency Drives (VFDs), relying instead on simple controls such as an on/off switch.
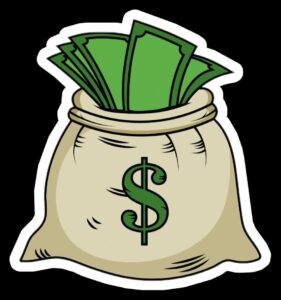
Consistent Performance
- ACBs deliver steady airflow and pressure, allowing system designers to size units accurately without oversizing to account for variability. SCFs, by design, generate inconsistent airflow, pressure, and energy usage, adding complexity and cost to system planning.
Customizable Waste Handling
- If valuable materials need to be collected, ACBs can be configured to direct particles into customizable collection units, tailored to the space available. This flexibility reduces installation costs compared to SCF systems with manufacturer-specific collection components.
A Smarter Choice for Air Purification
With their simplified design, lower costs, and superior energy efficiency, Air Cleaning Blowers™ provide a more practical and cost-effective solution for industrial air management compared to compressed-air-based filter systems.